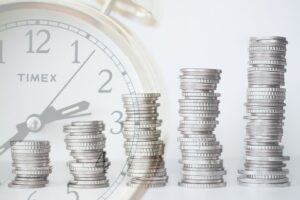
Scales, TCO, and the manufacturing industry go hand in hand.
When working in a business that requires the use of a scale for production, you’ll have to carefully keep watch on the TCO. TCO, or total cost of ownership, essentially is a financial term that involves calculating the total costs of all capital goods that the business produces. Having a TCO that is extremely accurate is the best way to evaluate how much money your business is losing from production costs each period and is also an essential step in determining overall profit. Believe it or not, certain models of high-powered scales can help automate the process of determining TCO by accurately measuring products to eliminate any bad ones. Here’s how!
How Calculation of TCO Increases Investment Potential
Calculation of TCO is very important in the manufacturing industry to maximize profits and eliminate unnecessary production costs. Here are four ways that using TCO to your advantage can help reduce costs effectively:
- Preventing Recalls, such as in the meatpacking or food manufacturing industry. By making sure all products are quality and manufactured exactly the same way, expensive recalls can be prevented before they have to occur.
- Reducing Waste/By-Products, such as avoiding product overflow which cannot be reused or recycled.
- Unnecessary Corrections, such as manufacturing errors or measurement inaccuracy leading to product defects.
- Protecting the Brand’s Safety, such as when a product defect or faultiness causes a public relations-related nightmare.
Thankfully, all of this can be minimized or even completely prevented by installing scales capable of calculating errors when they occur to make the total TCO accumulation much more accurate at the end of the sales period.
Difference between TCO and LCC
LCC, or life cycle costing, is a term that is commonly confused with TCO. However, the two are actually quite different when it comes to the calculation process. LCC only focuses on the operation and procurement costs as a result of manufacturing. TCO focuses on all aspects of LCC but also takes much more into account, such as employee training, downtime, and routine or unexpected maintenance costs. TCO also must be calculated based on an exact, uniform calculation process, whereas LCC can be calculated using more simplistic, estimated terms of loss.
TCO and Scales Calculation
As TCO requires a great amount of both qualitative and quantitative empirical data to be measured properly, a scale is a great way to start with the basics. Scales meant for determining TCO can help ensure that product measurements are extremely accurate to the smallest decimal but also record any abnormal downtime or maintenance periods to be used in the overall computation of TCO when needed for that particular sales period.
CONTACT THE SCALE PEOPLE FOR TCO ALIGNED SCALES IN NORFOLK, VA!
Since 1956, The Scale People have earned a reputation as the finest service provider for calibration and repairs of weighing equipment in the mid-Atlantic area. Our sales team can help work with you to find the best weighing equipment for your application. We currently have offices in Columbia, MD, and Newport News, VA, but we offer our services nationwide. Over the years, we have built up a long list of satisfied clients from a wide variety of industries, including pharmaceutical, food and beverage, and government manufacturing. We are a fully ISO/IEC 17025:2017 accredited service company. All of our services have a 100% satisfaction guarantee. We’re only a phone call away at +1 (800) 451-9593. To learn more about what we do, follow us on Facebook, Twitter, and LinkedIn.